De passies van Pirre | 25-augustus-2020 |
Alleen simpele oplossingen werken
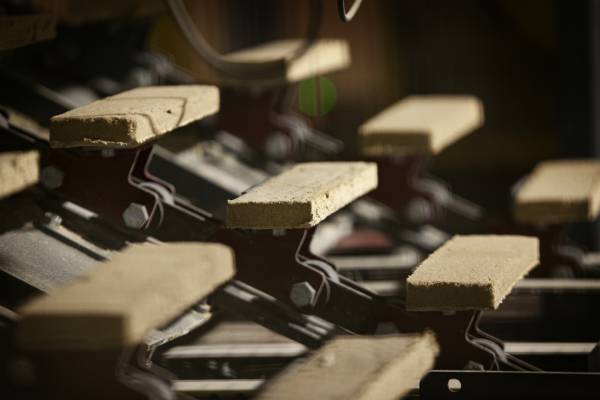
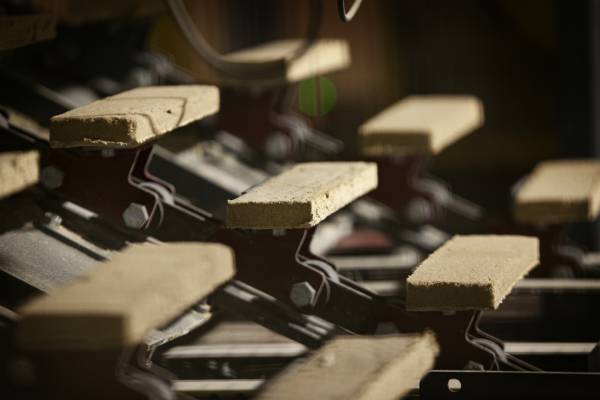
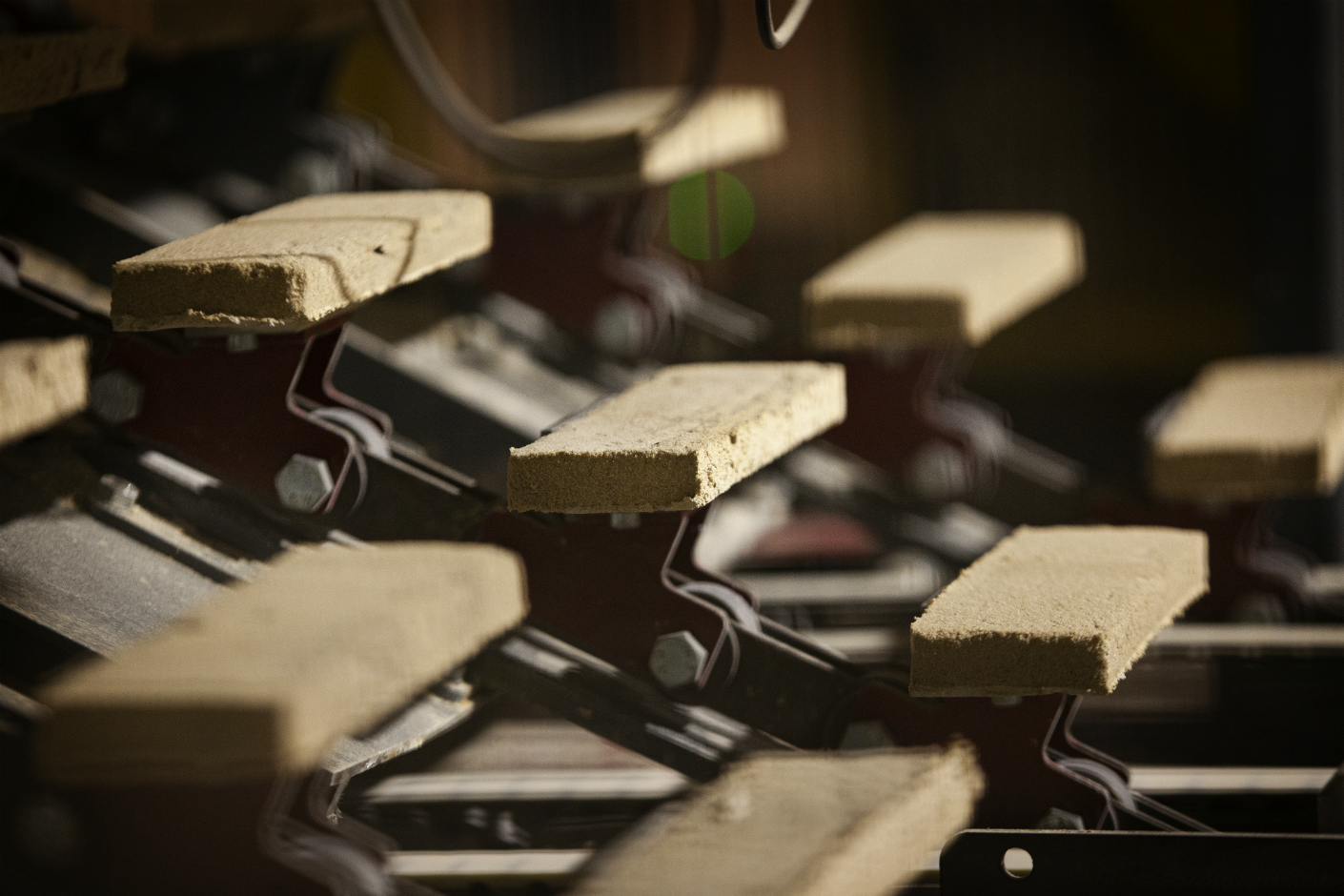
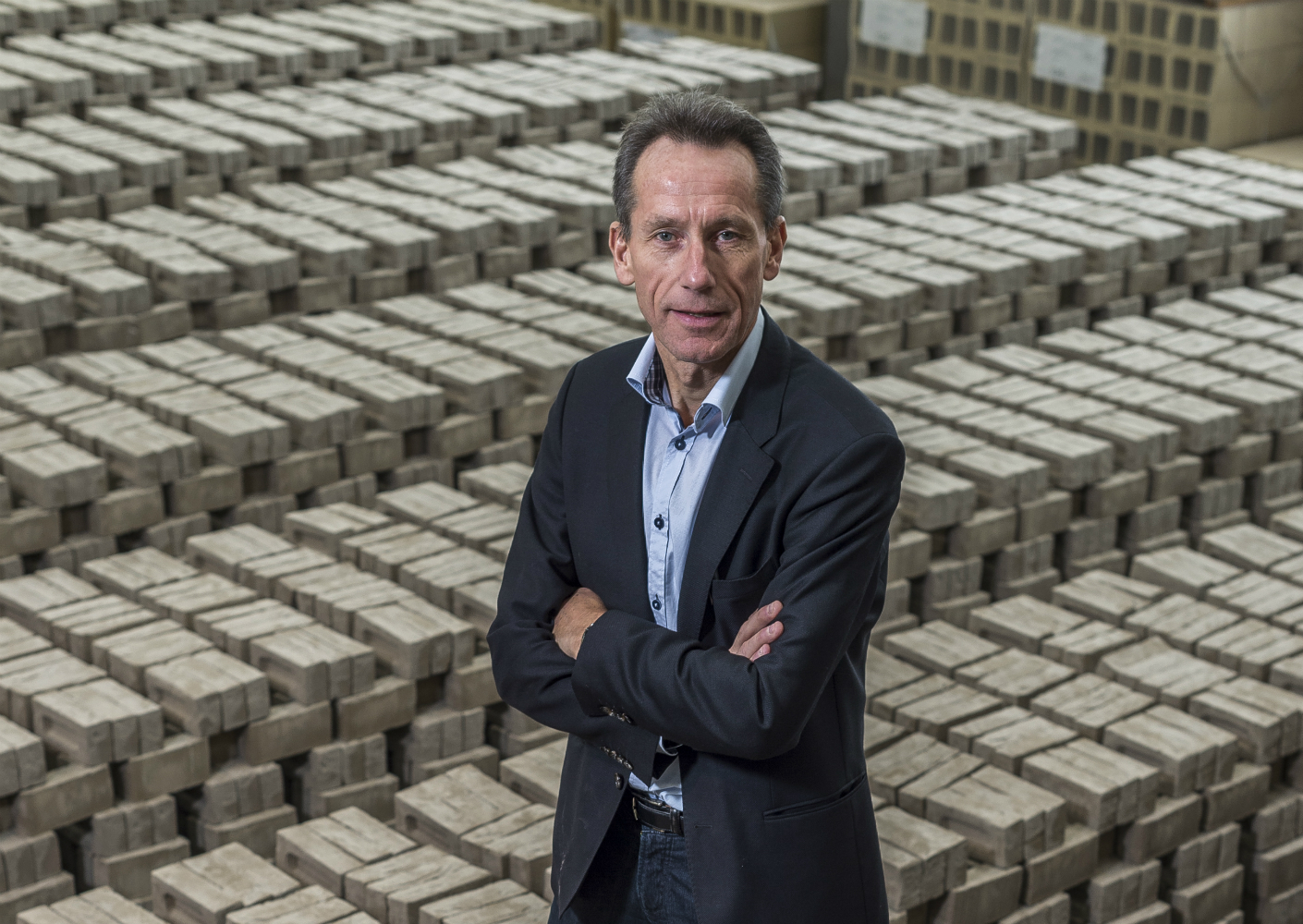
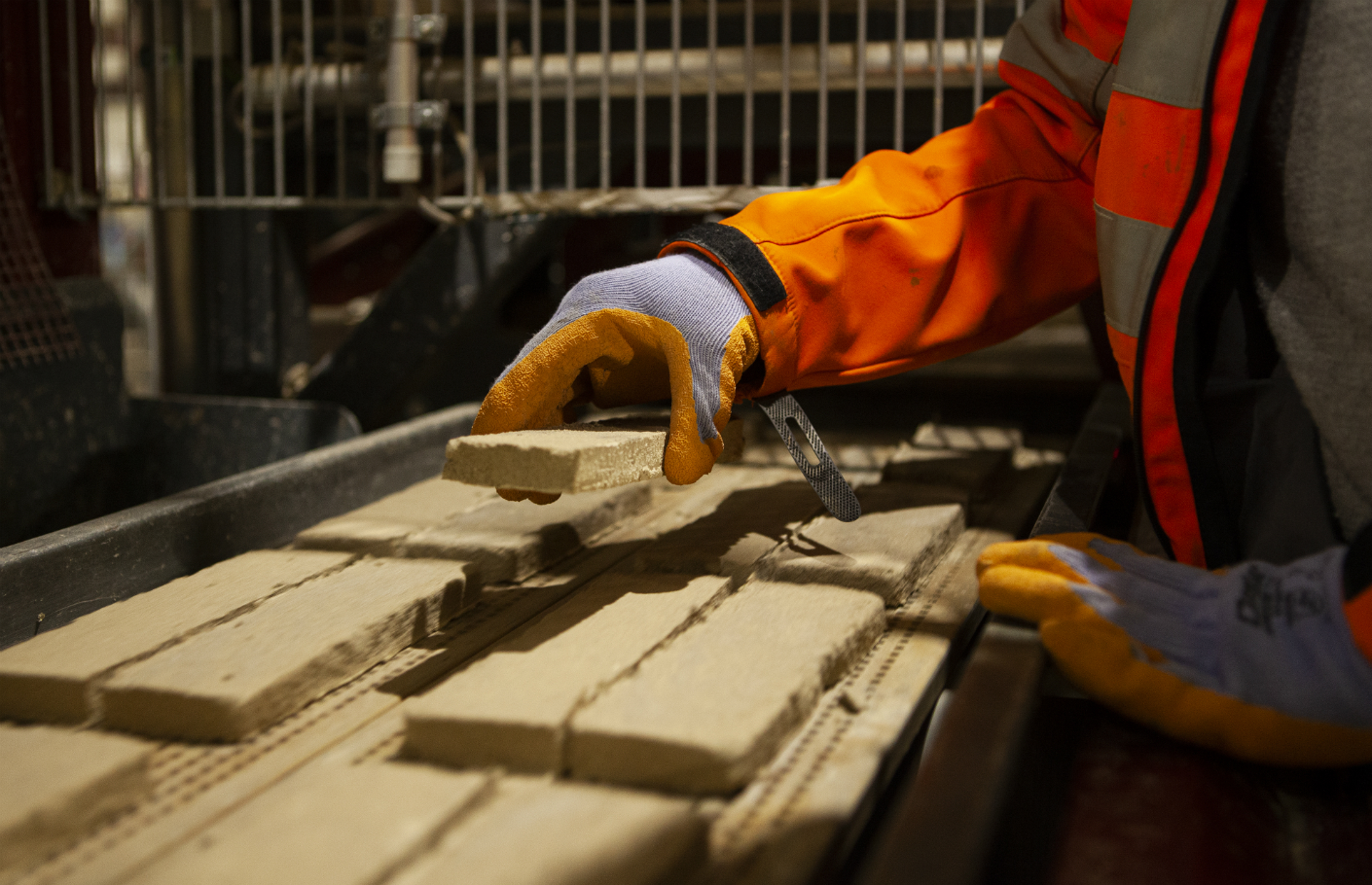
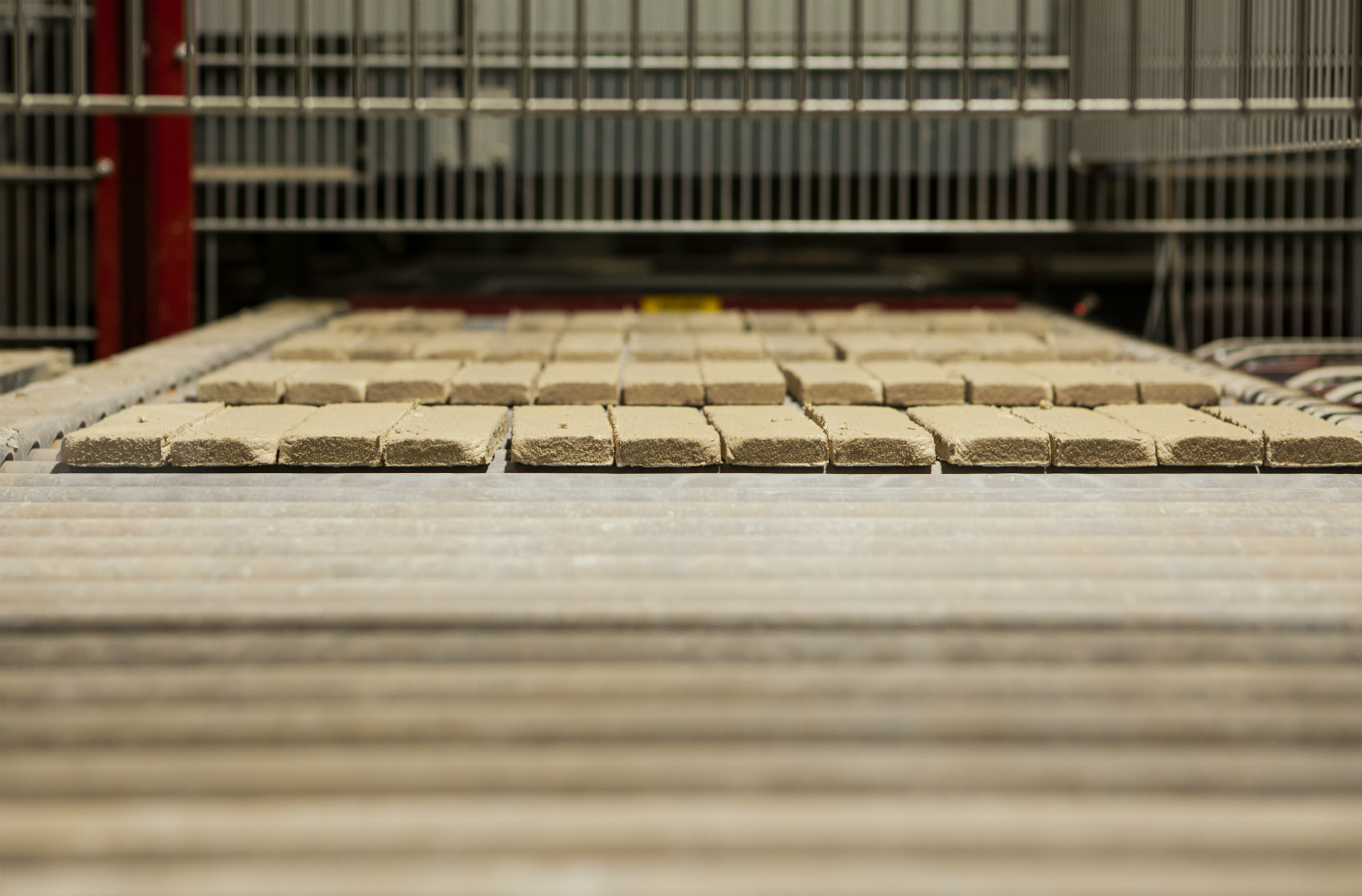
In de afgelopen tien jaar is Jean-Pierre (“Zeg maar Pirre”) Wuytack, CEO van Vandersanden Group, in toenemende mate gepassioneerd geraakt door alles wat met de transities ten gevolge van de klimaatdeal te maken heeft. Energie, en hoe de baksteenindustrie daarmee om kan gaan; groene energie; en CO₂-opslag en -toepassing. Naar aanleiding van zijn blog “Het einde van het bakstenen tijdperk? Energietransitie in de baksteensector” beantwoordde hij een aantal vragen.
Is dit het einde van de keramische gevelsteen?
“Willen we in 2050 nog bakstenen produceren, dan moeten we dat volgens de Green Deal met een grote CO₂-reductie doen. Eerst was er sprake van reductie van 80 %, maar met de nieuwste green deal is dat zelfs zero emission.”
Het vervaardigen van baksteen is een zeer energie-intensief proces. Niet alleen het bakken van de stenen bij 1000 tot 1200 °C, maar ook het drogen van de klei kost veel energie. Op dit moment wordt hiervoor nog aardgas verstookt, waardoor bij de productie van baksteen veel CO₂ vrijkomt. Het is duidelijk dat de traditionele keramische gevelsteen zo niet aan de eisen van 2050 kan voldoen.
Slank, slanker, slankst
In de zoektocht naar antwoorden op het klimaatvraagstuk onderscheidt Vandersanden twee fasen: van de hoeveelheid CO₂-uitstoot drastisch verlagen voor 2030, tot zero-emission in 2050.
In de eerste fase is het terugdringen van de CO₂-uitstoot het makkelijkst te bereiken door de energie-uitstoot van de gevel- en straatsteenproductie en van het product te beperken. Een traditionele gevelbaksteen is zo’n 10 cm (muur)breed, maar door de baksteengevel op dieet te zetten en op te bouwen uit dunnere gevelbakstenen, is al veel energie te besparen. Terwijl collega’s voornamelijk inzetten op “dematerialisatie” van de baksteengevel, met dunnere gevelbakstenen van 8 of 6,5 cm breed, zet Vandersanden volop in op de ontwikkeling van slanke baksteen strips van slechts 1,5 cm breed.
Van truweel naar lijmpistool
Een traditionele baksteengevel wordt gemetseld met vrij eenvoudige metselmortel op basis van zand en cement, die niet een heel hoge hechtingssterkte hoeft te hebben. Door het gewicht en de diepte van de stenen heeft de gevel al een behoorlijke stabiliteit en draagkracht, zodat er bijvoorbeeld zonweringen aan opgehangen kunnen worden. Bij een dunnere buitenschil zal gekozen moeten worden voor meer bevestigingspunten, of voor – door de buitenschil heen – bevestigen aan het binnenspouwblad.
Een dunnere gevelsteen moet anders verwerkt worden. De stenen worden niet met de troffel (truweel in het Vlaams) gemetseld en gevoegd, maar gelijmd. Daarbij wordt alleen de lintvoeg, de horizontale verbinding tussen de lagen, van een lijmlaag voorzien. De stootvoegen worden niet gelijmd. Doordat gewerkt wordt met een lijmpistool en doordat niet gevoegd hoeft te worden, kan tijdwinst worden behaald. Maar doordat de lintvoeg maar zo’n 3 tot 5 mm dik is, zijn 10 – 15 % meer stenen nodig. En omdat de lijmmortel tot vier keer duurder is dan standaard metselmortel, zijn de materiaalkosten wel hoger.
In Nederland is het verlijmen van gevelstenen nog geen gemeengoed, in tegenstelling tot in België, waar met name particuliere opdrachtgevers vallen voor de meer monolithische uitstraling van de gelijmde baksteengevel. Ook “architecten lopen d’r gek van”, aldus Wuytack.
Het productieproces gestript
Het nu gebruikelijke productieproces van baksteenstrips bestaat eruit dat hele gevelstenen worden gebakken, de steenstrips er afgezaagd worden en de rest wordt weggegooid of in het meest gunstige geval tot granulaat wordt verwerkt om aan nieuwe bakstenen toe te voegen of gebruikt te worden als steenslag voor funderingen.
In de nieuwe Vandersanden fabriek worden de ECO-baksteen strips rechtstreeks in mallen gevormd en worden de gestapelde strips vervolgens in een tunneloven gebakken. Ten opzichte van het gebruikelijke productieproces levert een materiaalbesparing van ruim 80 % op, en een energiebesparing van 50 %. Door in een volgende fase ook het bakproces verder te optimaliseren kan waarschijnlijk nog een bijkomende energie besparing worden gerealiseerd.
Obstakelparcours voor baksteenstrips
Baksteenstrips worden verlijmd op isolatiemateriaal dat zich aan de buitenzijde van het binnenblad bevindt. Om te voorkomen dat vocht doorslaat, moet deze mortellijmlaag een waterdichte laag vormen. De meeste isolatiematerialen zijn waterafstotend. Vandersanden raadt aan om isolatie te kiezen die vocht ondoorlatend is. Vandersanden heeft al sinds 2011 een buitengevelisolatiesysteem (E-board®) met waterondoorlaatbaar EPS, met speciale waterdichte kantdichting met tand en groef die eventueel ingekomen water naar buiten afvoert, en speciale waterdichte mortellijm. De baksteenstrips zelf zijn wel poreus, die vormen geen waterdichte schil. Hoeveel water de baksteenstrip opneemt of doorlaat is door de waterdichtheid van de onderconstructie niet langer van belang.
In sommige Nederlandse gemeenten wordt bij ter plaatse verwerkte baksteen strips om garanties gevraagd dat in het verwerkingsproces alle handelingen exact volgens de normen uitgevoerd worden. Baksteenstrips die in de fabriek onder gecontroleerde omstandigheden in geprefabriceerde gevelelementen verwerkt zijn, kunnen zondermeer worden toegepast, evenals mechanisch bevestigde baksteenstrips.
De huidige mechanische bevestigingssystemen voor baksteenstrips zijn gemaakt van metaal. In de baksteenstrips wordt een sleuf uitgespaard of ingefreesd, waarmee de strip op de metalen drager geschoven kan worden. De kleine baksteenstrips vereisen een fijnmazige ophangconstructie. Daardoor, en doordat de ophangconstructie van metaal is, zijn dergelijke systemen praktisch onbetaalbaar.
De weg naar zero-emission en circulair is niet zonder hobbels
Bouwproducten zullen in 2050 niet alleen zero-emission, maar ook circulair zullen moeten zijn. Een gemetselde of gelijmde traditionele of keramische baksteen kan theoretisch best zonder CO₂-uitstoot geproduceerd worden, maar die is dan nog niet circulair: tot gevel gemetselde of gelijmde bakstenen zijn niet demontabel en dus niet (makkelijk) hoogwaardig her te gebruiken.
Door gebruik te maken van elektrische steenovens, zou zonne-energie of windenergie gebruikt kunnen worden om keramische bakstenen zonder CO₂-uitstoot te bakken. De benodigde groene energie voor dezelfde hoeveelheid volle bakstenen zou dan echter vijf keer zo duur zijn, als voor aardgasgestookte ovens. Hierdoor zouden zero-emission gevelbakstenen zichzelf bij voorbaat uit de markt prijzen.
Zero-emission steenstrips zijn wél mogelijk voor dezelfde energiekosten, omdat het bakken van een steenstrip van 1,5 cm in een elektrische rolleroven maar circa één vijfde van de energie kost ten opzichte van volle bakstenen. Dan nog zijn op isolatie verlijmde steenstrips niet circulair, want niet eenvoudig demontabel en herbruikbaar.
Haalbaar, betaalbaar, circulair en zero-emission
De opdracht die Vandersanden zichzelf heeft gesteld is eenvoudig: een hoogwaardige keramische gevelbekleding, haalbaar, betaalbaar, circulair en zero-emission. “Wij hebben oplossingen, die niet alleen haalbaar zijn, maar die ook betaalbaar gaan zijn. En zij móeten circulair zijn.”
Wuytack gelooft stellig, dat alleen eenvoudige oplossingen werken. Om met keramische gevelbekleding tot circulair en zero-emission te komen, is er volgens hem maar één logisch recept:
- de keramische gevel van de toekomst moet zo slank zijn, dat hij met groene energie kostenneutraal gebakken kan worden,
- hij moet volledig demontabel en herbruikbaar zijn, om circulair te zijn en
- samen met het ophangsysteem mag het totaal niet duurder zijn dan een gemetselde gevel.
Voilà: de gevelstrippan. Een groter element met 5 – 6 steenstrips, in de mal gevormd op 1,5 cm dik in diepte, gebakken in een elektrische oven op groene energie, dus zero-emission. Opgehangen aan de gevel aan houten panlatten, geborgd met 1 schroef per element. Keramiek gaat honderden jaren mee en door dat schroefje is de gevelstrippan volledig demontabel en herbruikbaar, dus circulair. Een bewezen techniek, die met dakpannen al veel langer wordt toegepast, dus haalbaar. En met minimaal verbruik van materiaal en energie, dus betaalbaar. De eerste proeven zijn veelbelovend, maar het proces en de productie moet in de komende jaren nog verder uitgerold worden.
Zon en wind worden niet duurder
“De zon blijft schijnen, de wind blijft waaien, wordt niet duurder.” Wuytack zíngt het bijna. Door de technologische vooruitgang wordt het rendement van groene energieopwekking steeds gunstiger. Inmiddels kan er op de Noordzee met windparken al zonder subsidie windenergie worden opgewekt. De energieprijzen van groene energie zijn nu nog altijd ongeveer vijf keer hoger dan die van energie die opgewekt is met fossiele brandstoffen, maar door CO₂-taks en het stijgen van de prijzen van fossiele brandstof naarmate de voorraad daarvan afneemt, zal het uiteindelijk goedkoper zijn om groene energie te gebruiken.
Groene energie heeft wel veel ruimte nodig, omdat de energie-intensiteit veel lager is dan die van fossiele brandstoffen. Maar de installaties gaan lang mee, en de “brandstof” – zon en wind – is oneindig aanwezig en gratis.
Gelukkig is Europa als eerste ervan overtuigd dat het anders moet en heeft daar met de klimaatakkoorden een tijdspad voor uitgestippeld. Uiteindelijk zullen alle fossiele brandstoffen worden uitgeput, en zullen andere landen moeten volgen.
CO₂ kost te weinig
Om de transitie van grijze naar groene energie haalbaar te maken is er een factor, waarmee te weinig gerekend wordt: de prijs van CO₂. Nu is die ongeveer 20 à 25 euro per ton. Om veel van die nieuwe technologische oplossingen economisch haalbaar te maken, zou de prijs per ton CO₂ uitstoot 100 tot 200 euro per ton moeten zijn. Dan worden alle toepassingen van fossiele energie zo duur, dat groene energie gebruiken het enige economisch haalbare alternatief is. CO₂-prijs is de sleutel tot succes van groene energie.
Wuytack: “Zolang de CO₂-rechten nog (gedeeltelijk) gratis weggegeven worden, werkt het systeem nog niet goed. Europa kan het ook niet alleen. Om oneerlijke concurrentie te voorkomen, zouden landen die niet meedoen aan de klimaatdoelstellingen, waar geen CO₂-heffing wordt geheven bij import in de EU een CO₂-taks aan de grens moeten betalen, even hoog als hetgeen de Europese fabrieken betalen per ton uitgestoten CO₂. Daarmee voorkom je ook concurrentievervalsing, wanneer in Europa wel zero-emission geproduceerd wordt, met duurdere groene energie. Men kiest dan ook makkelijker voor lokaal geproduceerde producten. Dit is een beslissing die door de politiek genomen moet worden.”
EU ETS en de prijs van CO₂In de Europese Unie bestaat sinds 2005 een ‘cap and trade’ systeem (ETS) voor broeikasgassen, waaronder CO₂. ‘Cap’ wil zeggen, dat er een per deelnemend bedrijf een maximum wordt bepaald, ‘trade’ betekent dat de uitstootrechten onderling verhandeld (kunnen) worden. Wanneer een bedrijf niet meer uitstoot dan de “benchmark”, krijgt het even zoveel gratis uitstoot-rechten. Wanneer een bedrijf het maximum wel overschrijdt, moet het emissierechten bijkopen. Het doel moet zijn dat het goedkoper is om minder uit te stoten, dan om emissierechten bij te kopen. Om te voorkomen dat bedrijven hun productie verplaatsen naar landen buiten de EU waar niet met CO₂-emissiehandel wordt gewerkt (een fenomeen dat ‘carbon leakage’ wordt genoemd), krijgen bedrijven in sectoren waar het risico daarop groot wordt geacht, veel gratis emissierechten. In sectoren waar het risico op ‘carbon leakage’ verwaarloosbaar wordt geacht, moeten ze veel emissierechten bijkopen. Op de website van de Nederlandse Emissieautoriteit is een infographic te downloaden, waarin het hele systeem in beeld wordt gebracht. |
CO₂-vangen
Carbon Capture Storage (CSS), het opbergen van uitgestoten CO₂, en Carbon Capture Utilisation (CCU), het vastleggen van CO₂ in een product, zijn ook passies van Pirre. Voor een deel van het energieverbruik zal ook in de toekomst gebruik gemaakt worden van fossiele brandstoffen, vooral bij industriële centra en grote havens. Hier zal CO₂ moeten worden afgevangen en met pijplijnen naar opslagvoorzieningen moeten worden geleid. Dat kan bijvoorbeeld in de onderzeese aardgasvelden onder de Noordzee, waar al het aardgas al uit is. De CO₂ wordt dan in poreuze gesteenten gestopt – in hetzelfde gesteente waar eerder aardgas uitgehaald is. Dat vergt gigantische investeringen, maar de technologie is er al. Wuytack verwacht dat circa 80 % van de uitgestoten CO₂ met CCS zal moeten worden opgeslagen. Onder zee, in Noorwegen, of in de aardgasvelden in Groningen.
Van residu naar bouwmateriaal
Maar voor een deel kan de uitgestoten CO₂ met CCU worden vastgelegd. Dat is wat Vandersanden wil doen: CO₂ die afgevangen wordt – uit eigen steenfabrieken of van andere CO₂-uitstotende processen – gebruiken voor het maken van een nieuw bouwmateriaal.
Dit zou o.a. kunnen op basis van Carbinox, een restproduct uit de staalproductie dat voornamelijk calciumoxide en silicaten bevat. Door toevoeging van CO₂ kan op die manier een keiharde synthetische kalksteen worden gemaakt, waarin de opgenomen CO₂ voor eeuwig wordt vastgelegd.
Circulair en CO₂-negatief
Anticiperend op een stijging van de CO₂-prijs heeft Vandersanden reeds in 2016 het patent gekocht voor de productie van gevelstenen op basis van het eerdergenoemde CCU procedé. De Vandersanden Carbstone-gevelsteen wordt aldus CO₂-negatief, en zal ook in circulaire toepassingen ingezet kunnen worden. Niet mooier of beter dan een keramische gevelsteen – want níets is mooier of beter dan een keramische gevelsteen volgens Wuytack – maar haalbaar, betaalbaar, circulair en CO₂-negatief.
Een mogelijke eerste fabriek voor de Carbstone-gevelsteen, een pilotfabriek, zal alleen maar verliesgevend zijn. Vandersanden hoopt dan ook in aanmerking te komen voor een gedeeltelijke financiering door het EU Innovation Fund. Daarmee wordt het wel haalbaar om met traditionele baksteen te kunnen concurreren.
Binnen 10 jaar moet de technologie dusdanig verbeterd zijn, dat de productie daarna wél kostendekkend kan zijn. Pas bij opschaling naar meer fabrieken kan het product ook winstgevend geproduceerd worden.
De baksteensector vindt zichzelf opnieuw uit, met Vandersanden voorop
Tien jaar geleden had Wuytack het nog niet voor mogelijk gehouden dat de baksteenindustrie deze maatregelen zou kunnen overleven, maar door het productieproces en de producten aan te passen ziet hij zeker toekomst voor de steenfabrikanten. Dunnere buitenschil, zero-emission en circulair: dat zijn de bouwstenen waarmee de steenindustrie kan overleven.
“De eerste ecologische keramische 'in de mal gevormde' (= handvorm en wasserstrich) steenstripfabriek ter wereld is verlieslatend. ... Met de kleine capaciteit betaalt de investering voor die nieuwe fabriek zich nooit terug.” Wuytack: “Een multinational doet dat niet. Vandersanden is een familiebedrijf, met de filosofie dat het bedrijf de wereld niet kapot mag maken, maar een bijdrage moet leveren om de wereld te verbeteren. Als familiebedrijf zijn we er voor de volgende generatie. We willen producten maken die aan alles beantwoorden, met zero-emission, circulair. Dat heeft een prijs. Alles wat we verdienen, wordt opnieuw in het bedrijf geïnvesteerd. In vorige jaren in overnames en nieuwe fabrieken, maar vanaf nu voor een groot deel in nieuwe technologieën. Geen uitbreidingen meer in keramische gevelstenen, hooguit in ovens die zuiniger zijn en natuurlijk in het onderhoud van onze assets.”
En Pirre zelf?
De pensioengerechtigde leeftijd komt eraan en daarmee het einde van zijn loopbaan als CEO van Vandersanden. Maar Wuytack denkt er niet aan om afscheid te nemen van de baksteenindustrie. Hij wil zich blijven inzetten voor het uitdragen van deze duurzame boodschap voor de gehele baksteensector - als ambassadeur voor een betere wereld door circulaire gevelstenen, voor het heruitvinden van de baksteensector met als motto “liever samen met, dan solo slim”.